A first image has been released depicting the UK’s combat air flying demonstrator, as component deliveries and assembly work advance at BAE Systems’ Warton site in Lancashire.
Described by the airframer as employing a “cropped delta” configuration, the twin-engined design is due to be flown for the first time later this decade.
Officials stress that the developmental asset – which has yet to be given an official product name – is not a prototype for the next-generation fighter to be produced via the Global Combat Air Programme (GCAP) for Italy, Japan and the UK. It will, however, play an important role in de-risking a range of technologies that will be employed on that future operational platform; already named Tempest by the UK.
Key features of the demonstrator include a wide fuselage, which is required to accommodate internal weapons bays, and twin vertical tails. The aircraft’s nose section, meanwhile, resembles that shown on early concept models of the Tempest fighter.
Small engine intakes, meanwhile, sit ahead of internal serpentine ducts: a design characteristic supporting low observable performance on stealthy types.
Rolls-Royce has already tested a pair of Eurojet EJ200s, sourced from a Eurofighter Typhoon, which will be used to power the test platform. The demonstrator activity also involves guided weapons specialist MBDA, with more than 100 UK companies currently taking part overall.
Announced at the Farnborough air show in July 2024, the supersonic demonstrator will be the UK’s first such platform to be flown since the Eurofighter-precursor EAP, which made its debut in August 1986.
BAE is expecting the jet to be airborne “within three years” from now. While the jet “will be ready for first flight by the end of 2027”, it notes: “the exact date will be finalised nearer the time, to optimise learning and maximum benefit to GCAP”.
“We are well over two-thirds of the weight of the aircraft in the manufacturing and build stages,” says BAE platforms delivery director Paul Wilde.
A final set of carbon wing skins for the jet arrived at the company’s Warton site on 14 July, and “it is really starting to take shape across the wings, tails and main fuselage”.
“The size of some of the panels are really significant,” he says, referring specifically to the upper and lower wing sections, and a BAE-manufactured centre fuselage skin, which is the largest individual carbon component.
“Size causes its own challenge… in terms of being able to manufacture and transport all of that around,” he notes of the demonstrator’s early lessons.
While the design’s dimensions are not being disclosed, Wilde notes: “It is a large aircraft, in order to demonstrate some of the technologies required.”
“We are learning new things, and re-learning things that we had frankly forgotten,” says Tony Godbold, BAE’s future combat air systems delivery director, of the development activity.
He describes the aircraft as a “truly pioneering design with features that really define what a sixth-generation platform needs to be”.
“We are at an exciting phase with the aircraft taking shape,” he says, while noting that the use of a hot isostatic press technique to create complex shapes from powdered titanium is delivering “an order of magnitude saving” against traditional manufacturing methods.
“Where design parameters are really tight, being able to achieve complex shapes is going to be critical to the GCAP platform,” he says.
“The combat air flying demonstrator is providing invaluable lessons… and equipping our people with the skills they will need to deliver GCAP,” Richard Berthon, director future combat air at the Ministry of Defence, says of the UK-only activity.
Meanwhile, a headquarters for the three-nation GCAP activity was opened in Reading, Berkshire on 7 July. The facility hosts both the GCAP International Government Organisation and the Edgewing industrial joint venture between BAE, Japan Aircraft Industrial Enhancement, and Leonardo.
GCAP is intended to deliver an operational sixth-generation fighter and supporting systems for use from 2035.
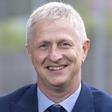